Today, the U.S. Department of Energy’s (DOE) Office of Fossil Energy (FE) and NETL have issued a request for information (RFI) to understand workforce development needs within the high-performance materials supply chain.
The advanced materials supply chain consists of four segments—alloy production, shaping, finishing, and component assembly. In the fossil energy industry, these segments create high-paying jobs and contribute to a secure energy supply in the United States. However, recent events and disruptions have shifted the focus of manufacturing needs.
A workforce skilled in additive manufacturing, novel joining and welding, robotics, and automated production is required to maintain and grow a robust advanced materials supply chain. This RFI seeks information to identify the most pressing workforce needs and gaps, match skills with employment needs, and establish training programs and curricula. The collected information/data will then be used to create a targeted workforce that can address immediate demands and strengthen lasting capacity for fossil fuel applications.
About
News and Events
Research and Programs
Carbon Management Point Source Carbon Capture Carbon Dioxide Removal Carbon Dioxide Conversion Carbon Transport & Storage Hydrogen with Carbon Management
Resource Sustainability Methane Mitigation Technologies Minerals Sustainability Natural Gas Decarbonization and Hydrogen Technologies Advanced Remediation Technologies Energy Asset Transformation
Key Lab Initiatives Advanced Alloys Signature Center (AASC) Science-based Artificial Intelligence and Machine Learning Institute (SAMI) Center for Microwave Chemistry (CMC) Center for Sustainable Fuels and Chemicals (CSFC)
Energy Technology Development Office of Energy Efficiency and Renewable Energy Battery Workforce Initiative Cybersecurity, Energy Security, and Emergency Response Office of ElectricityGrid Resilience
Business
Library
Explore our Library
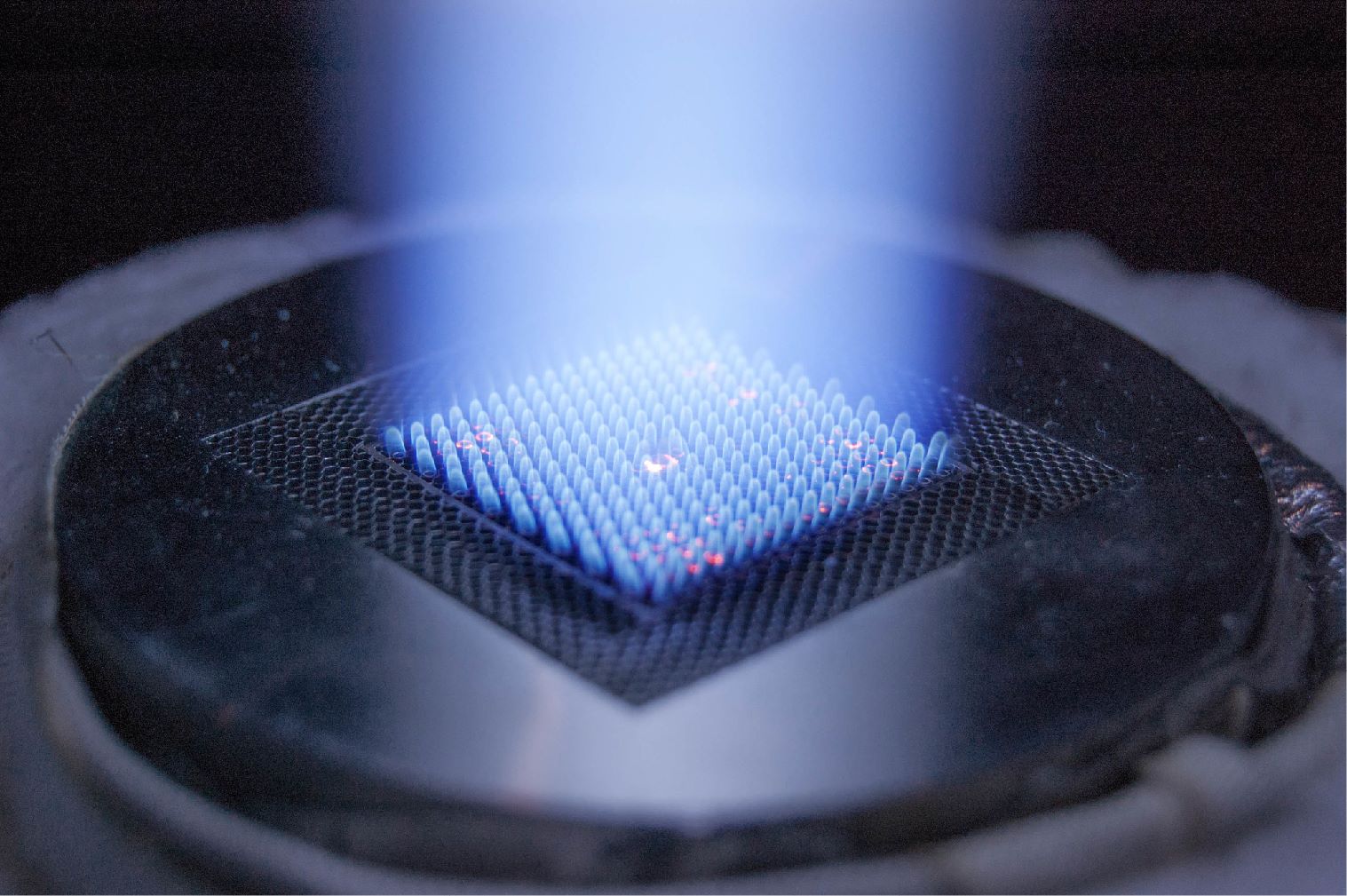
Approved Categorical Exclusions Environmental Assessments Environmental Impact Statements Oil and Gas Projects Summaries NETL Fact Sheets NETL Newsletters Publication Search Energy Data Exchange (EDX) FECM External R&D Final Technical Reports Summary Information for External R&D Awards Technical Reports Series (TRS) Peer Review Reports Interagency Working Group Initial Report
- Research and Programs
- Carbon Management
- Core Competencies
- Resource Sustainability
- University Training & Research
- Key Lab Initiatives
- Energy Technology Development
- Featured Infrastructure
- Methane Emissions Reduction Program
-
- Business
- Technology Transfer
-
- Library
- Energy Analysis
-
- About
- News and Events
- Education