Advanced Alloys Signature Center
About AASC
NETL’s Advanced Alloys Signature Center (AASC) is a complete alloy development facility capable of prototyping alloys at scales that advance commercialization. The AASC allows prototyping of diverse and specialty alloys at masses up to 500 pounds, a scale that is currently absent from the domestic alloy research and development ecosystem. Designed as an expansion to NETL’s existing ingot metallurgy capabilities at its site in Albany, Oregon, the AASC can prototype specialty alloys supporting advanced energy, defense, aerospace, automotive, chemical processing, and biomedical devices and technologies, all at a single research facility. Alongside industry partners, the facility will accelerate commercializing these advanced alloys—helping the U.S. maintain and grow global leadership in these industries.
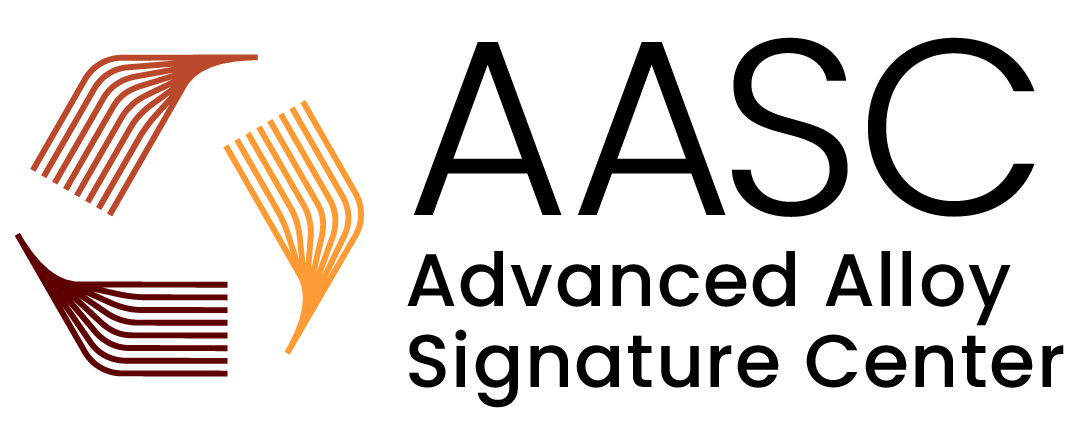
AASC Spotlight
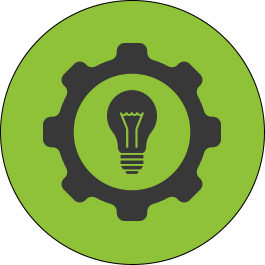
Facilities and Equipment
NETL invested more than $60 million in infrastructure and $12 million in new equipment at its Albany, Oregon, site including the purchase of a new, $1.3 million 500 lb. vacuum induction furnace (VIM). A planned additional $30+ million investment in the next three to five years includes an upgraded $15 million, 13,000 square foot state-of-the-art melting facility able to melt and process almost any alloy.
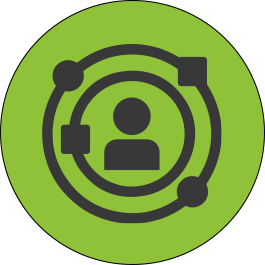
Experience
NETL’s alloy development capabilities are anchored by the lab’s alloy ingot metallurgy (melting) and thermal-mechanical processing (forging and rolling). Combined with computational materials design and performance evaluation, NETL can provide alloy solutions enabling advanced energy systems and supporting the deployment of emerging technologies for U.S. industry.
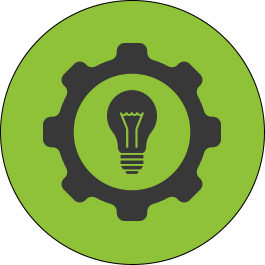
eXtremeMAT
NETL is the leading laboratory in eXtremeMAT, a partnership of seven U.S. DOE National Laboratories that collectively harness their unparalleled capabilities to accelerate developing materials for service in extreme environments.
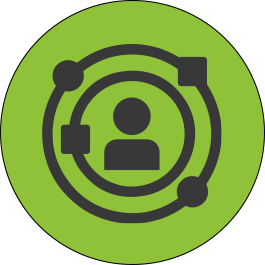
Collaboration
NETL’s alloy development capabilities are anchored by the lab’s alloy ingot metallurgy (melting) and thermal-mechanical processing (forging and rolling). Combined with computational materials design and performance evaluation, NETL can provide alloy solutions enabling advanced energy systems and supporting the deployment of emerging technologies for U.S. industry.
Our Unique Experience
NETL utilizes an integrated alloy development approach leveraging computational materials engineering, manufacturing at scale, and performance assessment at condition. Advanced alloy development capabilities include:
- Melt processing
- Air induction melting: up to 300 lbs.
- Vacuum induction melting: 10, 50, and 500 lbs.
- Vacuum Arc remelting, electro slag remelting: 3- to 8-inch diameter ingots, 50-500 lbs.
- Button melting: 50-500 grams
- Heat treatment & fabrication capabilities
- Heat-treatment furnaces: 1650°C, inert atmospheres and controlled cooling
- Press forge: 500 tons
- Hot and cold roll mills: 2 and 4 high configurations
NETL identifies and develops lower carbon footprint feedstocks spanning the entire hyrdogen value chain for a more agile supply chain, including advanced hydrocarbons, renewables (including biomass), electrification, and other low-carbon feedstocks supporting new investments.
We demonstrate and deploy alloys with improved performance capabilities for energy applications, aerospace, defense, and bio-medical applications. This includes:
- Laboratory capabilities to simulate real-world environments
- Severe environment corrosion/erosion research facility (SECERF)
- Corrosion and oxidation laboratories
- Fracture mechanics and creep capabilities
NETL leverages its expertise in computational modeling to advance the design and improve the capability to predict the performance of alloys in harsh environments needed to reduce the environmental impact of energy production. Alloy development has been a time-consuming process marked by repeated tests to achieve the desired component performance; computational modeling and developing simulation data represent the next step to close the design loop for rapid alloy development. Learn more.
NETL’s AASC is significantly investing in developing feedstock to support Big Area Additive Manufacturing (BAAM) and Wire Arc Additive Manufacturing (WAAM). The new equipment installed in the Oregon-based NETL facility extends the window of capability for drawing wire as it relates to the diameter, the material type, and the associated length for different feedstocks. The wire output from this process can also be used for profile matching for weld wire needs associated with ‘joining’ applications in more traditional process approaches.