In an effort that could lead to accelerated design and deployment of advanced energy systems, NETL researchers have added a valuable new capability to the Lab’s world-renowned Multiphase Flow with Interphase eXchanges (MFiX) modeling software suite. Rather than modeling particles as spheres, as is the case with most discrete element modeling (DEM) techniques, NETL researchers have developed and validated an algorithm to simulate non-spherical shapes that better approximates real-world particles, significantly increasing modeling accuracy.
Real-life granular materials such as coal and biomass are non-spherical in nature. However, researchers have long used simple spheres in DEM simulations to represent various interacting particles found in multiphase flow systems like fluidized beds, gasifiers and chemical looping reactors. While this technique is computationally efficient and allows for the simulation of hundreds of millions of particles necessary to model industrial-scale systems, it fails to adequately account for the gas-solid interaction in the reactor.
About
News and Events
Research and Programs
Carbon Management Point Source Carbon Capture Carbon Dioxide Removal Carbon Dioxide Conversion Carbon Transport & Storage Hydrogen with Carbon Management
Resource Sustainability Methane Mitigation Technologies Minerals Sustainability Natural Gas Decarbonization and Hydrogen Technologies Advanced Remediation Technologies Energy Asset Transformation
Key Lab Initiatives Advanced Alloys Signature Center (AASC) Science-based Artificial Intelligence and Machine Learning Institute (SAMI) Center for Microwave Chemistry (CMC) Center for Sustainable Fuels and Chemicals (CSFC)
Energy Technology Development Office of Energy Efficiency and Renewable Energy Battery Workforce Initiative Cybersecurity, Energy Security, and Emergency Response Office of Electricity
Business
Work with Us
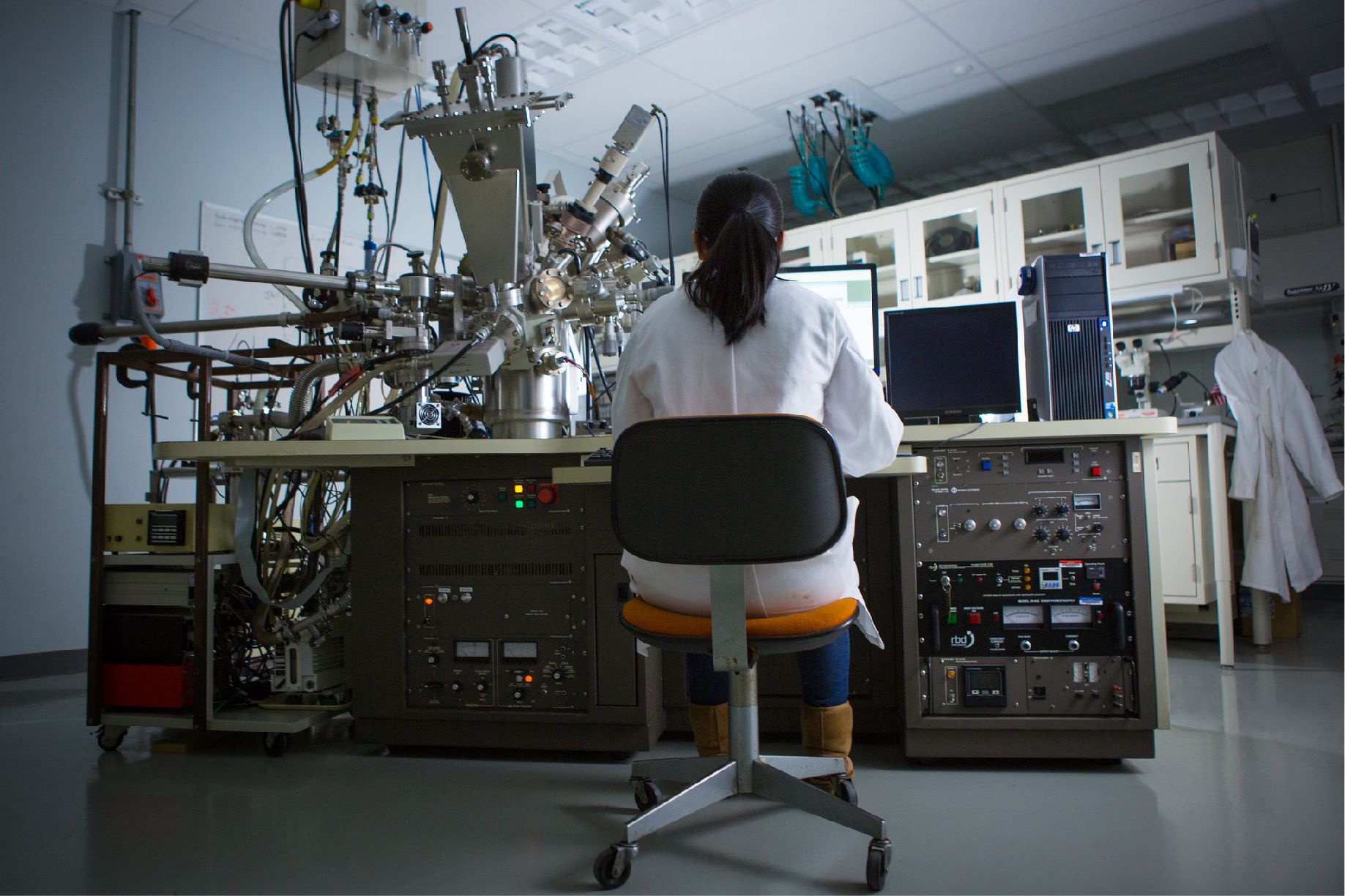
Library
Explore our Library
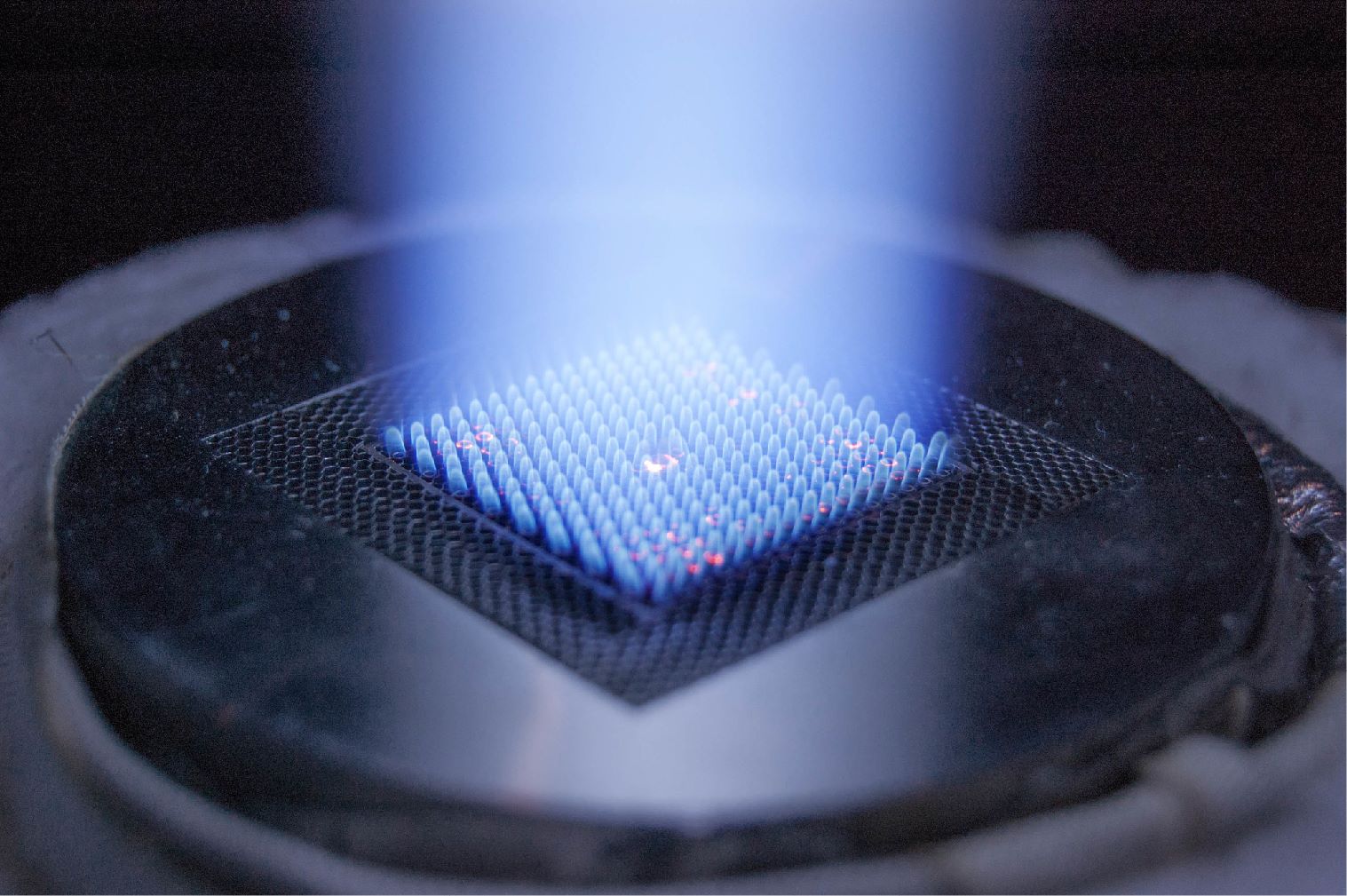
Approved Categorical Exclusions Environmental Assessments Environmental Impact Statements Oil and Gas Projects Summaries NETL Fact Sheets NETL Newsletters Publication Search Energy Data Exchange (EDX) FECM External R&D Final Technical Reports Project Landing Page Summary Information for External R&D Awards Technical Reports Series (TRS) Peer Review Reports
- Research and Programs
- Carbon Management
- Core Competencies
- Resource Sustainability
- University Training & Research
- Key Lab Initiatives
- Energy Technology Development
- Featured Infrastructure
- Methane Emissions Reduction Program
-
- Business
- Technology Transfer
-
- Library
- Energy Analysis
-
- About
- News and Events
- Education