About
News and Events
Research and Programs
Carbon Management Point Source Carbon Capture Carbon Dioxide Removal Carbon Dioxide Conversion Carbon Transport & Storage Hydrogen with Carbon Management
Resource Sustainability Methane Mitigation Technologies Minerals Sustainability Natural Gas Decarbonization and Hydrogen Technologies Advanced Remediation Technologies Energy Asset Transformation
Key Lab Initiatives Advanced Alloys Signature Center (AASC) Science-based Artificial Intelligence and Machine Learning Institute (SAMI) Center for Microwave Chemistry (CMC) Center for Sustainable Fuels and Chemicals (CSFC)
Energy Technology Development Office of Energy Efficiency and Renewable Energy Battery Workforce Initiative Cybersecurity, Energy Security, and Emergency Response Office of Electricity
Business
Library
Explore our Library
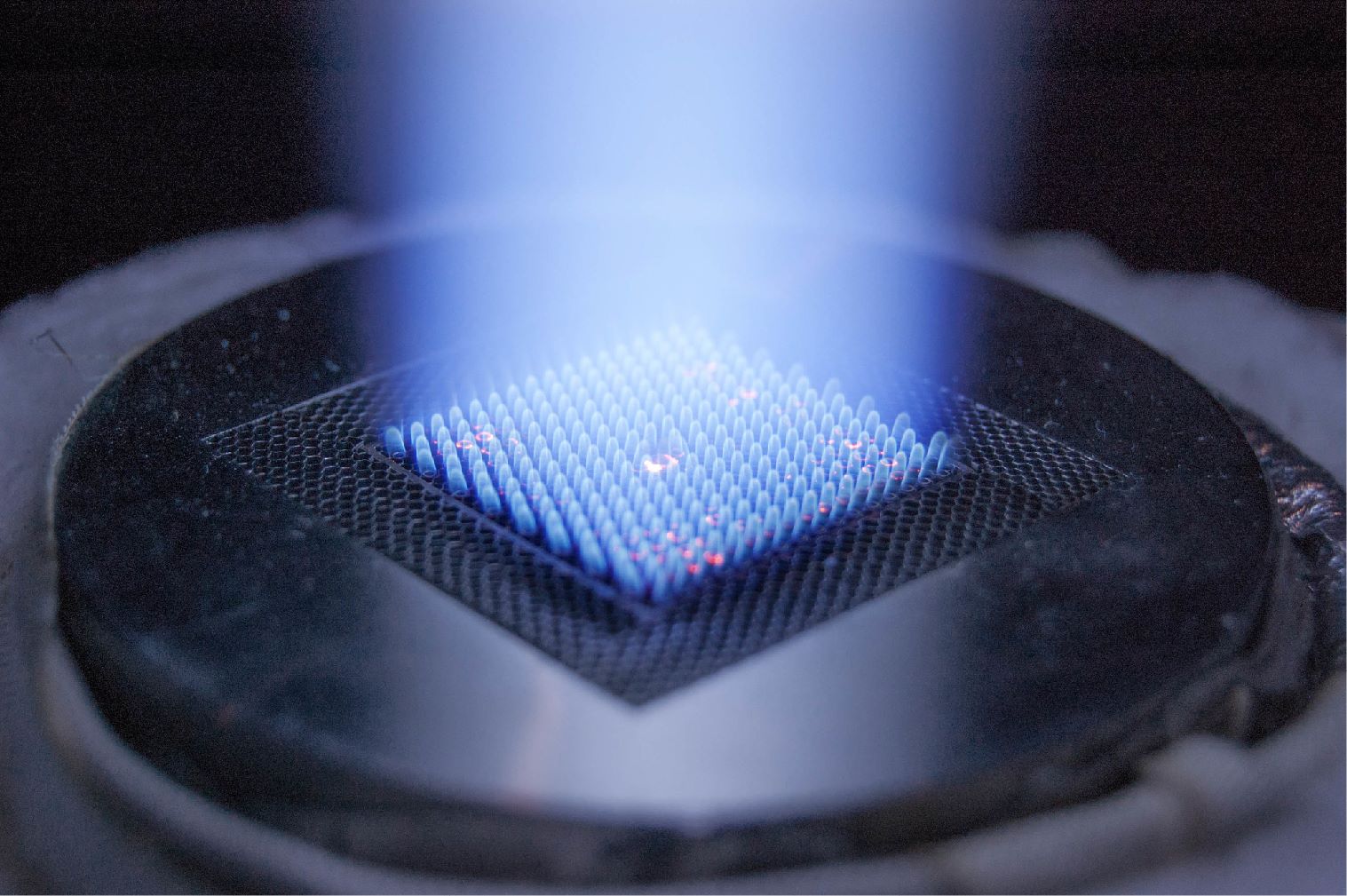
Approved Categorical Exclusions Environmental Assessments Environmental Impact Statements Oil and Gas Projects Summaries NETL Fact Sheets NETL Newsletters Publication Search Energy Data Exchange (EDX) FECM External R&D Final Technical Reports Project Landing Page Summary Information for External R&D Awards NETL R&D Publication Search Peer Review Reports
- Research and Programs
- Carbon Management
- Core Competencies
- Resource Sustainability
- University Training & Research
- Key Lab Initiatives
- Energy Technology Development
- Featured Infrastructure
- Methane Emissions Reduction Program
-
- Business
- Technology Transfer
-
- Library
- Energy Analysis
-
- About
- News and Events
- Education