Development of a Low-Cost Rotary-Steerable Drilling System
Project Number
DE-FC26-05NT42657
Goal
The goal is to develop and commercialize a 6 ½-inch rotary-steerable system (RSS) capable of drilling 7 7/8-inch to 9 7/8-inch hole sizes at conventional pressures and temperatures (20,000 psi and 150–175°C) that reduces operating costs by a minimum of 50% and lost-in-hole charges by at least 50% over currently offered systems.
Performer(s)
Diamondback Downhole Technologies LLC, Houston, TX 77099-4301 - Performer 2008 - 2011
Noble Wellbore Technologies, Inc., Sugar Land, TX 77478-3686 - Initial research 2005 - 2008
Background
One of the most significant advancements in the petroleum industry in recent years has been the development and application of rotary-steerable systems (RSS) that provide accurate directional control of the borehole via closed-loop steering. RSS offer several advantages over conventional directional bottom-hole assemblies that use positive-displacement motors (PDM). These include:
- Higher rates of penetration achieved by eliminating the significant amount of non-productive time with PDMs spent orienting and maintaining the tool face against reactive torque, along with the ability to deliver greater horsepower to the bit using the drilling rig’s top drive or rotary table.
- Maximizing the total length of extended-reach/horizontal well segments that can be drilled with RSS because drill-string drag is significantly lower when the pipe is continuously rotated rather than slid.
- Smoother boreholes (reduced tortuosity) that allow the casing to be run to the bottom in longer laterals than is the case in wells drilled with PDMs.
Rotary-steerable systems are complex devices that demand day rates 3 to 4 times higher than those for PDMs with measurement-while-drilling (MWD). RSS also possess much higher lost-in-hole exposure, with some systems approaching $1.5 million depending on the sensor suite. Higher rates paid to achieve the benefits cited above are justified for most offshore programs, but often prevent the use of RSS in many onshore drilling programs, particularly for lower-margin fields. Industry experts cite a required reduction in day rates to levels of 1.2 to 1.5 times the cost of PDM+MWD and a 50% reduction in lost-in-hole costs to achieve widespread use of RSS in U.S. onshore drilling programs. To achieve these cost reductions, it will be necessary to significantly change tool designs such that the costs to build and operate RSS can be greatly reduced.
Impact
The benefits of RSS for vertical control, directional drilling, and extended-reach laterals are well understood and appreciated within the oil and gas industry. Applications of today’s generation of RSS continue to expand and costs decrease with new entrants to the market. However, both the rate at which this is occurring and the overall percentage of onshore wells where RSS is employed remain low, primarily due to the high costs. The proposed technology has the potential to be used in up to 50 to 75% of vertical control/directionally drilled wells, both on- and offshore. The applications for cost-effective RSS will become increasingly more important as development transitions to deeper, more hostile, lower margin gas reservoirs. This technology has the potential to significantly reduce the cost of drilling the types of wells that will become increasingly more common as these resources are developed.
The design being developed by this effort has the potential to substantially reduce RSS costs on a number of fronts by:
- Lowering the cost to manufacture through a very low part count, simplification in number and complexity of machining operations required, and the use of limited lengths of expensive, high-strength, non-magnetic stainless steels.
- Lowering the cost to operate since there are no consumable elements used to produce electrical power.
- Lowering the cost to service since the number of moving parts is low, the electronics robust, and there will be a minimum number of elastomer seals and bearings to be replaced.
- Lowering the costs for logging-while-drilling (LWD) based on a decision to support operations with third-party LWD systems through a communications support structure afforded by a mode-based downlinking system.
Accomplishments (most recent listed first)
- Two prototype, low-cost, rotary steerable tools were successfully designed, fabricated, and laboratory tested.
- The prototype build costs are 55% less than the costs of the previous generation of Noble’s push-the-bit rotary steerable tools. This was achieved by applying the “lessons learned” from the Well Director field testing program along with the ability to start with a clean sheet of paper. The new generation low-cost RSS tools have 34 versus 70 subassemblies and less than ¼ of the total part count. This has been accomplished without any loss in system functionality.
- The servicing costs of the low cost rotary steerable tools are expected to be only 25% of that for the prior generation RSS tools. This has been achieved by reducing the soft parts (i.e., o-rings, fasteners, bearing, etc.) that need to be replaced after each job as well as reducing the number of assembly steps and the technician time required to complete these steps. Key subassemblies have been packaged for “plug and play”. They are (1) an integral hydraulic system; (2) an integrated electronics system where all items reside in a single BeCu pressure barrel; (3) easily serviceable steering pistons; and (4) use of 20,000 WPSIG rated electrical connectors that eliminate the need for wire soldering.
- All components were 100% inspected and successfully passed qualification testing prior to tool assembly and laboratory testing.
- The prototype LCRSS was flow tested on a rotary test stand for 101 hours. These tests were structured to fully exercise all system elements with the exception of borehole pressure which will be done once the field test program is initiated. The tests demonstrated the system to reliably operate as designed. They also identified a small number of “punch list” items that will be instituted and verified prior to well testing.
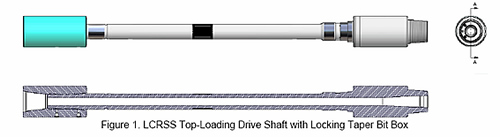
The objectives of reducing fabrication and low-in-hole costs were successfully met. The LCRSS prototype costs are 55% less than the prior generation tools. These costs are expected to be driven even lower in production due to economies of scale and the development of effective setup tooling accomplished during the prototype fabrication.
Servicing costs, based on the rapid turnaround time and substantial reduction in the number of soft parts that must be replaced after every run, are expected to be less than 25% of the costs for the prior generation Well Director tools. Typical rebuilds should be accomplished in under 12 man-hours.An inductive coupling system to transmit control signals and operating power across an air gap has been designed and developed.
The design of a hydraulic system was completed and manufactured. The hydraulic design is a closed-loop system with system oil to shaft oil piston compensation and is designed to generate operational pressures used by the steering pistons. High-pressure oil is used to deliver the desired force to the steering pistons for well path steering. Low-pressure oil is used to maintain a desired holding force on the steering pistons to prevent rotation of the housing relative to the well bore. The main drive shaft of the LCRSS powers the hydraulic pump, which supplies working oil pressure for the system. The design approach minimizes part count, especially for O-ring seals and fasteners. As importantly, this also allows the entire hydraulic assembly to be pre-assembled, evacuated, oil-filled, and performance-tested prior to installation onto the tool. Installation to the LCRSS housing is very straightforward. All electrical connections are made using one multi-pin boot connector running from the electronics canister to the hydraulic canister. The hydraulic canister is fastened to the tool housing using socket-head cap screws. Hydraulic communication with the four steering pistons is accomplished via hydraulic passageways running from the solenoid valve outputs to each of the pistons.
Current Status
(February 2011)
The project has been completed. The final report is available below under "Additional Information".