NETL’s STEM Education & Outreach Team supports all types of science, technology, engineering and math (STEM) learning — even if that learning takes place through a screen. Throughout the coronavirus pandemic of 2020 and into 2021, team members have stayed busy by preparing virtual activities and participating in online events that continue to bring STEM education, information on science career paths and more to students and science professionals during a time of great uncertainty.
In the last year, NETL developed the first in a series of virtual Meet A Scientist events to increase the accessibility of the Lab’s research and directly engage with K-12 students in Pennsylvania, West Virginia and rural Oregon. Interested participants submitted questions through NETL’s social media accounts, with researchers addressing selected questions through a live virtual event. Researchers were able to speak about their career pathways and exciting research roles during the event. Future Meet a Scientist events are slated to occur, so check NETL’s social media to learn about future dates and topics.
About
News and Events
Research and Programs
Carbon Management Point Source Carbon Capture Carbon Dioxide Removal Carbon Dioxide Conversion Carbon Transport & Storage Hydrogen with Carbon Management
Resource Sustainability Methane Mitigation Technologies Minerals Sustainability Natural Gas Decarbonization and Hydrogen Technologies Advanced Remediation Technologies Energy Asset Transformation
Key Lab Initiatives Advanced Alloys Signature Center (AASC) Science-based Artificial Intelligence and Machine Learning Institute (SAMI) Center for Microwave Chemistry (CMC) Center for Sustainable Fuels and Chemicals (CSFC)
Energy Technology Development Office of Energy Efficiency and Renewable Energy Battery Workforce Initiative Cybersecurity, Energy Security, and Emergency Response Office of Electricity
Business
Work with Us
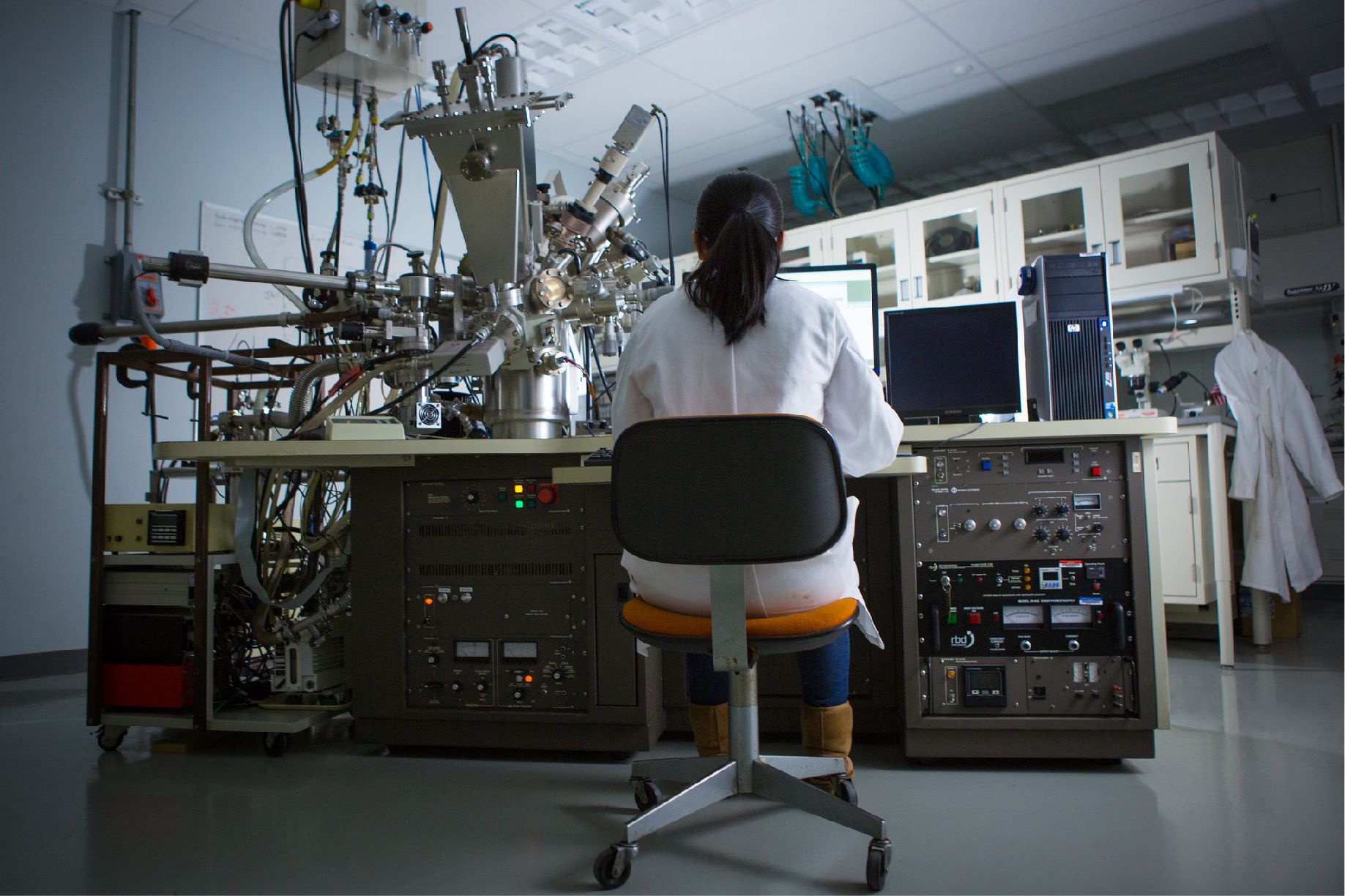
Library
Explore our Library
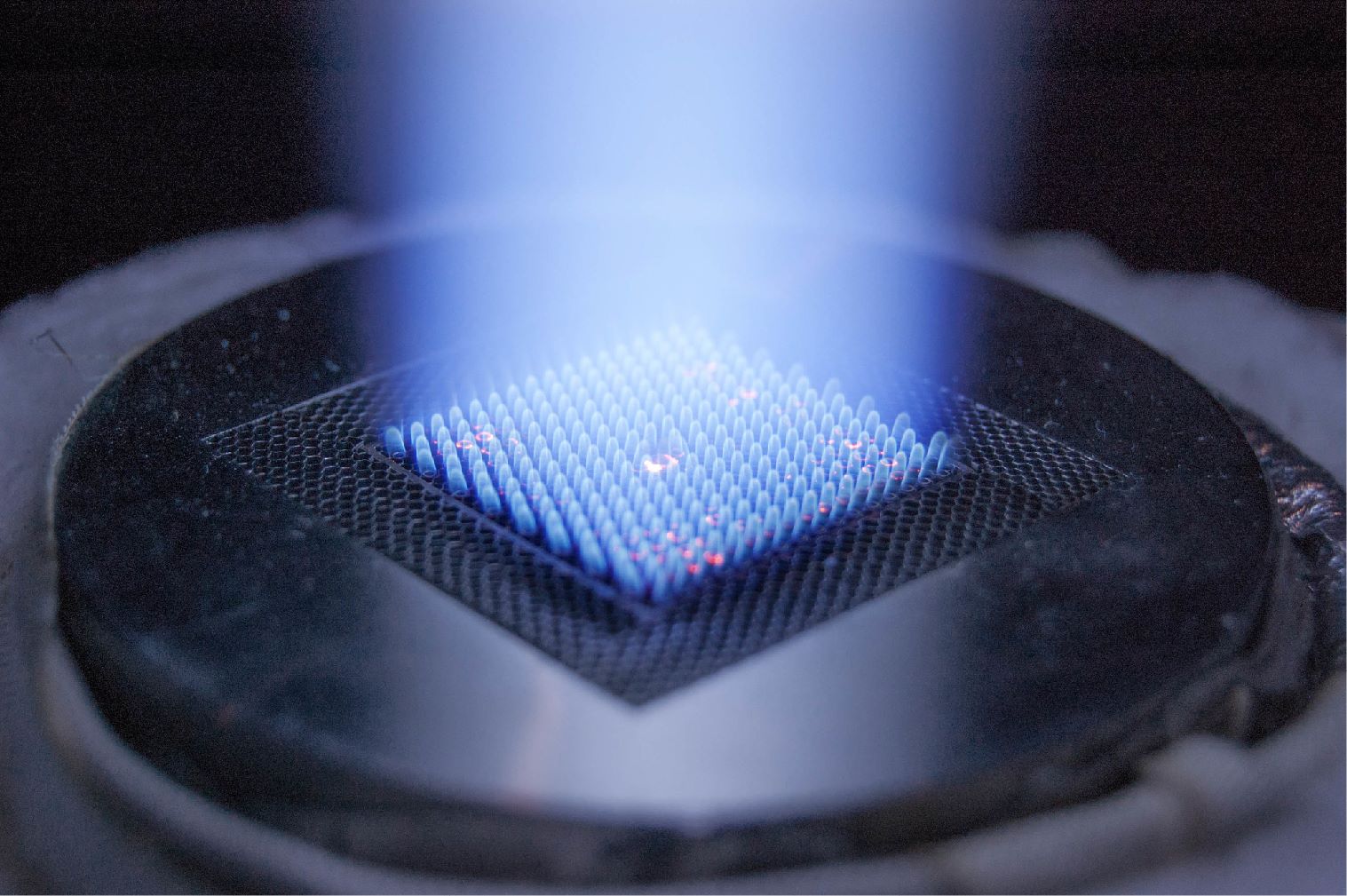
Approved Categorical Exclusions Environmental Assessments Environmental Impact Statements Oil and Gas Projects Summaries NETL Fact Sheets NETL Newsletters Publication Search Energy Data Exchange (EDX) FECM External R&D Final Technical Reports Project Landing Page Summary Information for External R&D Awards Technical Reports Series (TRS) Peer Review Reports
- Research and Programs
- Carbon Management
- Core Competencies
- Resource Sustainability
- University Training & Research
- Key Lab Initiatives
- Energy Technology Development
- Featured Infrastructure
- Methane Emissions Reduction Program
-
- Business
- Technology Transfer
-
- Library
- Energy Analysis
-
- About
- News and Events
- Education