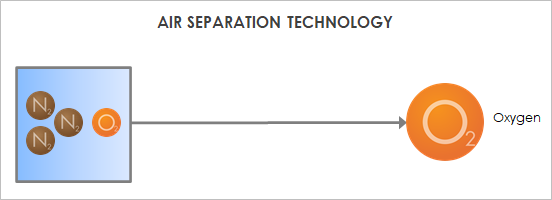
Air Separation Technology focuses on identification of new concepts and technologies for production of oxygen for use in gasification systems. Oxygen-blown gasification powerfully facilitates high-quality syngas and hydrogen production, and most gasification-based energy systems inherently run more efficiently if the oxidant is oxygen rather air. However, gasification systems have traditionally relied on conventional cryogenic air separation, which is expensive both in terms of capital expenditure and cost to operate, and which demands relatively large scales. Accordingly, the technologies under development target low cost, high levels of operational efficiency, and modular scale capability. Fields of investigation under Air Separation Technology currently include:
- Advanced Membranes
- Ceramic Membranes (ion transport)
- Innovative Concepts
- On-site NETL Research (oxygen carriers/sorbents)
Philosophy
The historical context for development in this area was oxygen production for large integrated gasification combined cycle power plants (e.g., by scaling up high-temperature ceramic membrane-based ion transport membrane technology). This has shifted to innovative technologies that can deploy in concert with modular gasification-based systems targeted for valuable fuels, chemicals and hydrogen production. NETL continues to be interested in developing innovative air separation technology, including new formulations/configurations of membranes enabling higher efficiency, advantageous operating conditions, or reduced costs, use of solid oxygen carriers in looping configuration to provide in-situ oxygen production in gasifiers, and innovative concepts including magnetic field-based air liquefaction.
Strategy
The Gasification Systems Program plans to continue to develop air separation technologies to be utilized in advanced energy systems for high-value production from coal and solid fuels. Consistent with the overall program strategy, technological development of air separation systems will be suitably sized for integration in modular gasification systems. The program continues a nonrestrictive strategy of fostering technology advancement in any air separation technology area, from cryogenic to innovative concepts, if potential for cost reduction and performance advancement exist.
Advanced Membranes
The portfolio includes multiple projects developing novel membrane systems:
Ceramic Membranes
At suitably elevated temperatures, certain formulations of ceramic membranes are permeable only to oxygen ions and are therefore 100% selective. Examples have included OTM (oxygen transport membranes) and ITM (ion transport membranes), which have undergone significant development (notably by Praxair and Air Products). At temperatures of 1450-1650°F, oxygen from feed air adsorbs on the membrane and dissociates to form oxygen ions by electron transfer. The oxygen anions enter and migrate through the ceramic lattice countercurrently with electrons and are driven toward the permeate side by the oxygen partial pressure differential that can be established variously by pressurizing the feed air, establishing vacuum on the permeate side, or gas sweeping the permeate side. Ceramic membrane systems afford the opportunity of integrated operation with turbines, and their operation at elevated temperatures increases efficiency/reduces parasitic energy penalty compared to conventional cryogenic oxygen production systems. Systems analyses on a variety of gasification-based processes have shown significant cost and efficiency advantages compared to conventional cryogenic technology; however, technical issues with membrane life, durability of system components, and manufacturing yield continue to be problematic. Approaches such as identifying different materials including dual or mixed matrix ceramic materials that can operate at more moderate temperatures (1100-1300°F) with suitable flux, and membrane configurations and engineering to improve durability and operational integrity of air separation modules, and application to smaller, modular systems have developmental promise.
Sorbents
The portfolio includes projects involving the development of innovative sorbents for air separation:
Innovative concepts
The portfolio includes an interesting project that s applying the magnetocaloric effect for refrigeration/liquefaction of air. This approach uses solid state refrigerants, involving minimal gas compression and no expansion refrigeration (saving the capital and operating costs of turbomachinery).
On-site NETL Research — Air Separation:
NETL has been developing oxygen carrier materials for possible use in both stand-alone oxygen production modules, and in production of in-situ oxygen within oxygen generation reactors. These carrier materials have tunable oxygen delivery properties to respond to a variety of opportunities and fuels. Investigations are providing information about the link between composition and carrier performance with a focus on use of these materials in modular reactor systems.
- Process Development To Mature Oxygen Sorbent-Based Technology — This task features development of a computational model that captures the storage and release potential of oxygen for the NETL-designed oxygen carrier materials, and deployment of the model for simulation of a pilot-scale fixed-bed, perovskite sorbent oxygen separation reactor, including capture and regeneration modes of operation with system thermal management. Model predictions will be validated with experimental data, including data from a bench-scale oxygen reactor, which will provide invaluable insights on performance and costs of this type of air separation system.
- Maturing Oxygen Carrier and Catalyst Technologies for Hydrogen Production — NETL is developing optimized systems with carbon capture that can be used in hydrogen production from solid fuels, such as biomass, plastics, or municipal solid waste. Two novel patented/patent-pending processes are being pursued: an iron-based catalytic process and a metal ferrite-based noncatalytic process. Information and parameters are being identified for use in developing integrated hydrogen production systems, a scaled-up reactor design based on subpilot-scale and pilot-scale test data, and for supporting technoeconomic analyses and commercialization.
Systems Analyses
As part of the support for Air Separation key technology, systems studies are being conducted to provide unbiased comparisons of competing technologies, determine the best way to integrate process technology steps, and predict the economic and environmental impacts of successful development.
Other key technologies within Gasification Systems include the following: