CO2 Capture from Ethanol Facilities | CO2 Capture from Iron and Steel Production | CO2 Capture from Cement Plants | CO2 Capture from Hydrogen Production
Point source carbon capture from industrial sources (e.g., chemical production [ammonia, hydrogen, petrochemical], mineral production [cement and lime], natural gas processing, and iron and steel production plants) separates carbon dioxide (CO2) emissions from the plant’s flue gas or other exhaust stream that would otherwise have been released to the atmosphere. As the U.S. industrial sector accounted for over 1,300 million tonnes of CO2 emissions in 2020[i], the deployment of point source capture technologies from industrial sources is a vital element in reducing CO2 emissions.
The U.S. Department of Energy/National Energy Technology Laboratory’s (DOE/NETL) Point Source Carbon Capture Program is supporting engineering-scale testing and front-end engineering design (FEED) studies on carbon capture technologies that separate at least 95% of the total CO2 emissions at industrial facilities. Furthermore, NETL is addressing challenges with the application of carbon capture, utilization and storage (CCUS) to steam methane reforming (SMR) and autothermal (ATR) plants, such as increased levelized cost of hydrogen at high carbon capture rates, increased natural gas consumption, and/or reduced amounts of electricity, through initial engineering designs of commercial-scale, advanced CCUS systems that separate and store or utilize CO2, with 90% carbon capture efficiency, from SMR or ATR plants producing high-purity hydrogen from natural gas. The complexity of capturing CO2 from industrial sources varies across the sector with CO2 concentrations greatly depending on the industry and the specific stream targeted for CO2 capture. Industrial sources that have a highly concentrated stream of CO2, such as natural gas processing, fertilizer production, hydrogen production, and ethanol production, have lower energy requirements for CO2 separation. For lower-concentration industrial sources, such as iron and steel production, cement manufacturing, and petroleum refining facilities, significant challenges exist in developing carbon capture technologies, including energy requirements, differing gas compositions, varying process temperatures and pressures, and various contaminants.
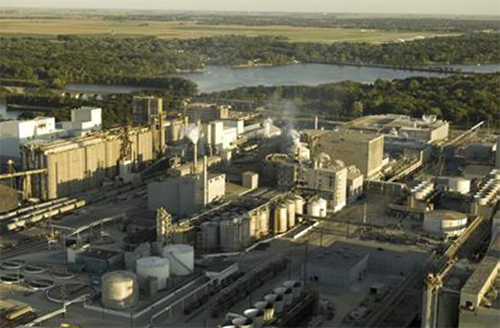
Archer Daniels Midland’s Agricultural Processing and Biofuels Plant in Decatur, Illinois; CO2 Capture from Biofuels Production and Storage into the Mt. Simon Sandstone.
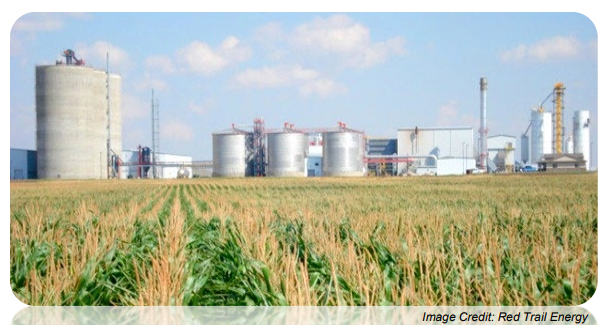
Red Trail Energy’s ethanol plant in Richardton, North Dakota.
CO2 Capture from Hydrogen Production
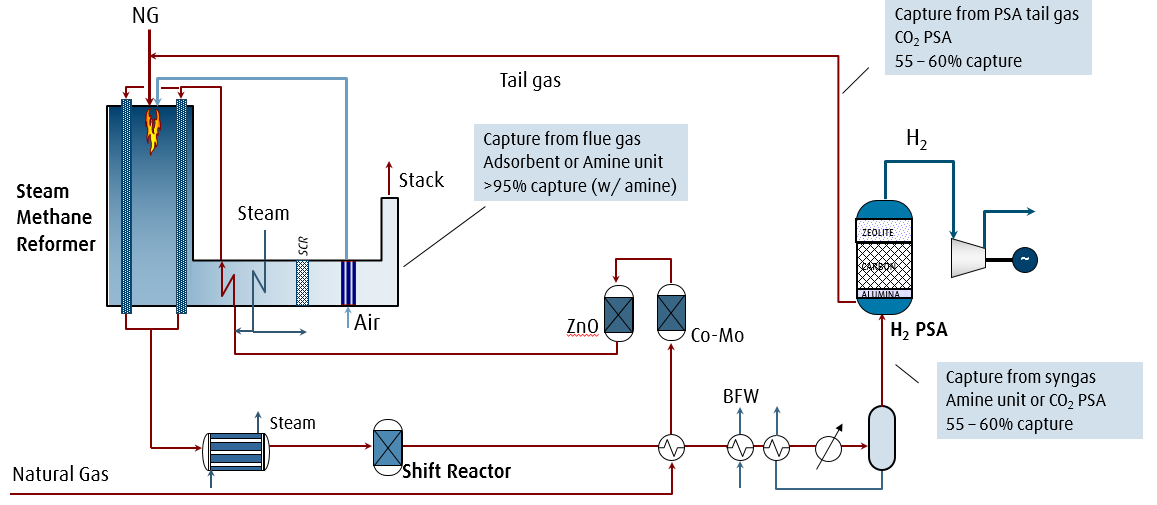
Schematic of hydrogen production via steam methane reforming with various CO2 capture options.
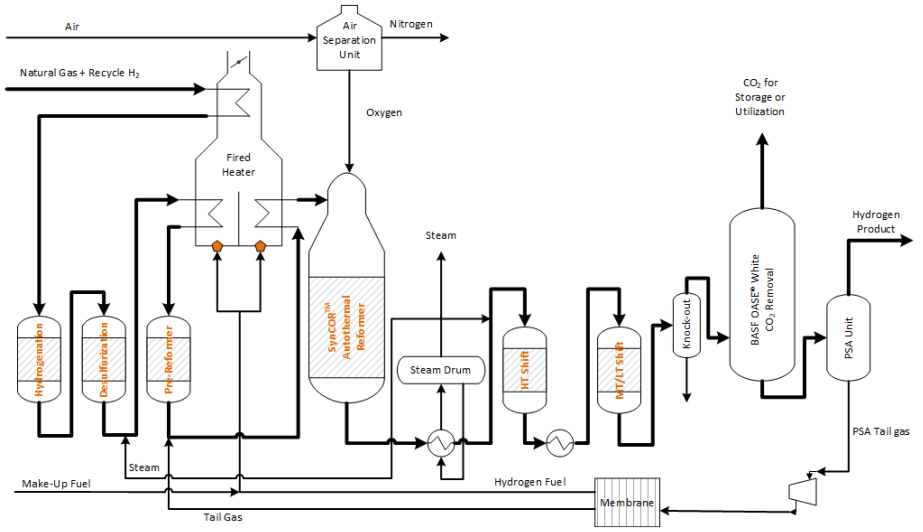
Schematic of hydrogen production via autothermal reforming with CO2 capture.
Hydrogen production via steam methane reforming (SMR) involves reacting natural gas and steam to produce synthesis gas (syngas), a mixture of carbon monoxide and hydrogen gas. A water-gas shift reaction may be performed to increase the amount of hydrogen gas in the product gas which also increases the concentration of CO2 in the shifted syngas. Hydrogen production emits CO2 from the process gas and from the combustion of natural gas (flue gas). When producing hydrogen via SMR, there are three separate point sources in which CO2 can be collected or vented from the plant: from the SMR flue gas, from the syngas stream before pressure swing adsorption (PSA), and from the PSA tail gas. In autothermal reforming (ATR) plants, either highly pure oxygen from an air separation unit (ASU) or input air is added to partially oxidize the natural gas, producing hydrogen-rich syngas. The autothermal (internal) combustion process in ATR plants results in a higher concentration of CO2 in the syngas than in the flue gas. Since CO2 capture from flue gas is considerably more expensive and complex (low CO2 partial pressure, N2/O2 impurities) than from syngas, it is more economical to capture the CO2 from the syngas stream prior to entering the PSA unit in an ATR plant.
Through a U.S. Department of Energy (DOE)-funded project led by Air Products and Chemicals, Inc., two SMR hydrogen production plants located within the Valero Refinery in Port Arthur, Texas were successfully retrofitted with vacuum swing adsorption systems to separate the CO2 from the process gas stream. The process concentrates the CO2 in the reformer process gas stream from 10-20% to greater than 97% CO2 purity, while capturing more than 90% of the CO2 in that stream[iii].
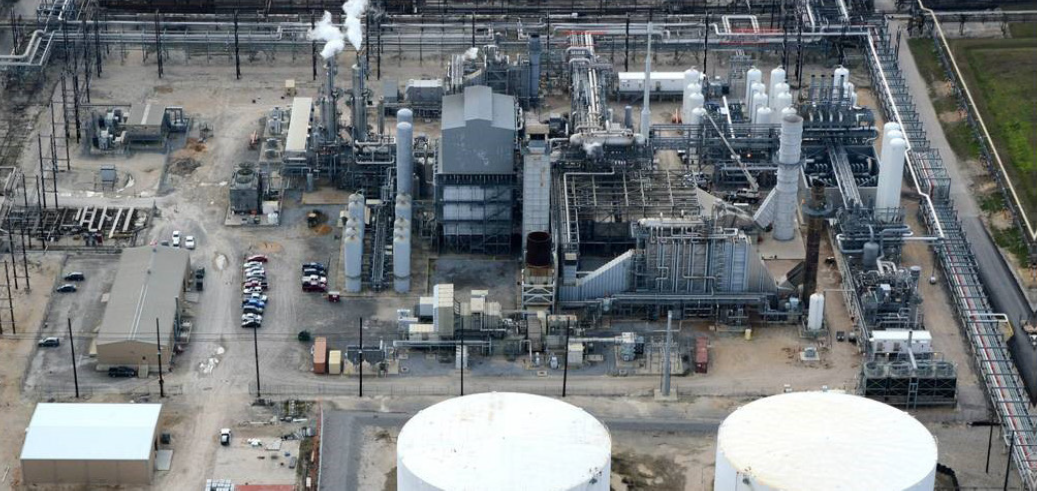
Air Products and Chemicals Inc.’s refinery in Port Arthur, Texas.
[i] U.S. Energy Information Administration. U.S. Energy-Related Carbon Dioxide Emissions, Monthly Energy Review. https://www.eia.gov/totalenergy/data/monthly/pdf/sec11.pdf
[ii] “Cost of Capturing CO2 from Industrial Sources.” National Energy Technology Laboratory. January 10, 2014. ESPA Authoring Template (doe.gov)
[iii] “Air Products and Chemicals, Inc.: Demonstration of CO2 Capture and Sequestration of Steam Methane Reforming Process Gas Used for Large-Scale Hydrogen Production.” National Energy Technology Laboratory. July 2017. https://www.netl.doe.gov/sites/default/files/netl-file/FE0002381.pdf