NETL in the news
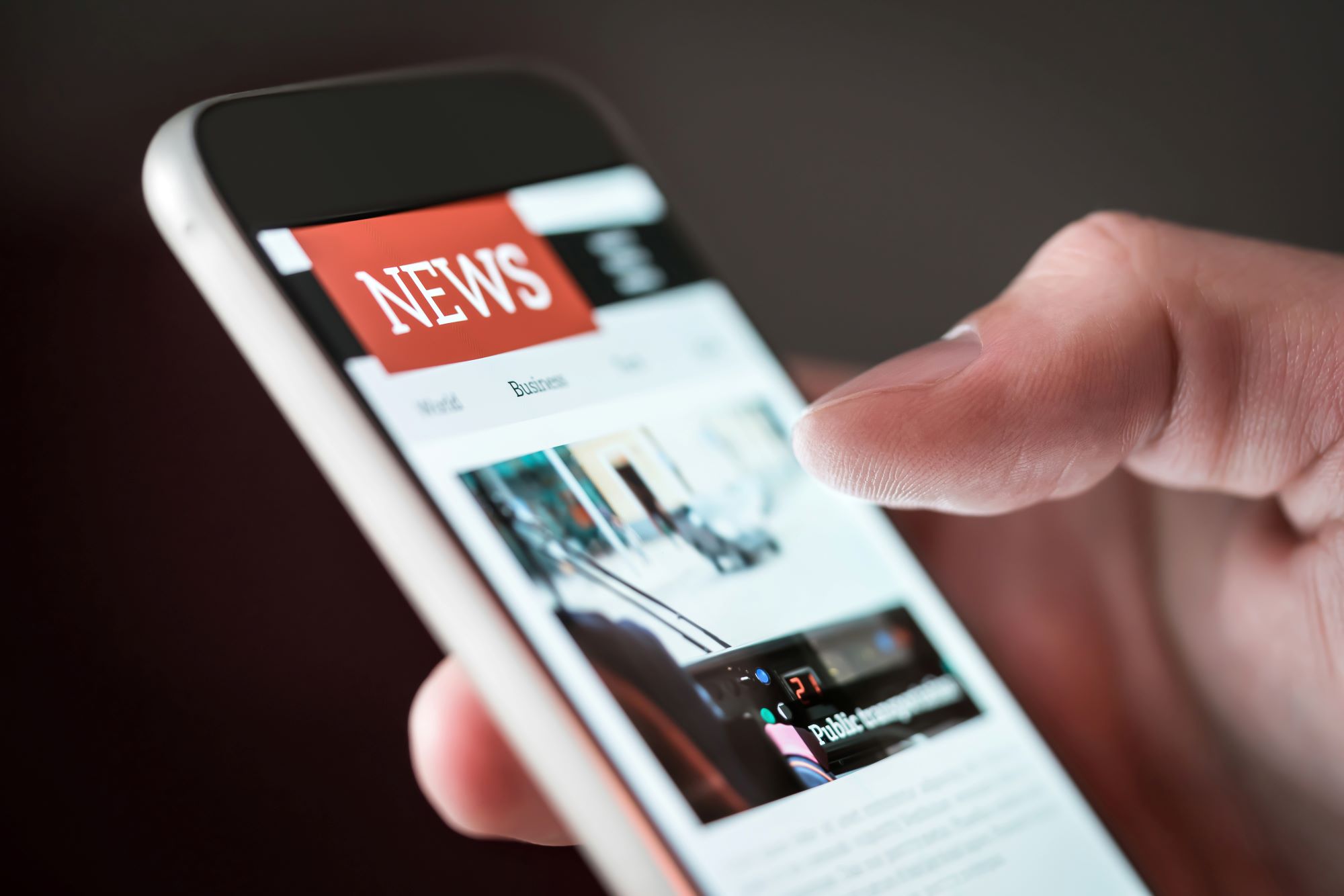
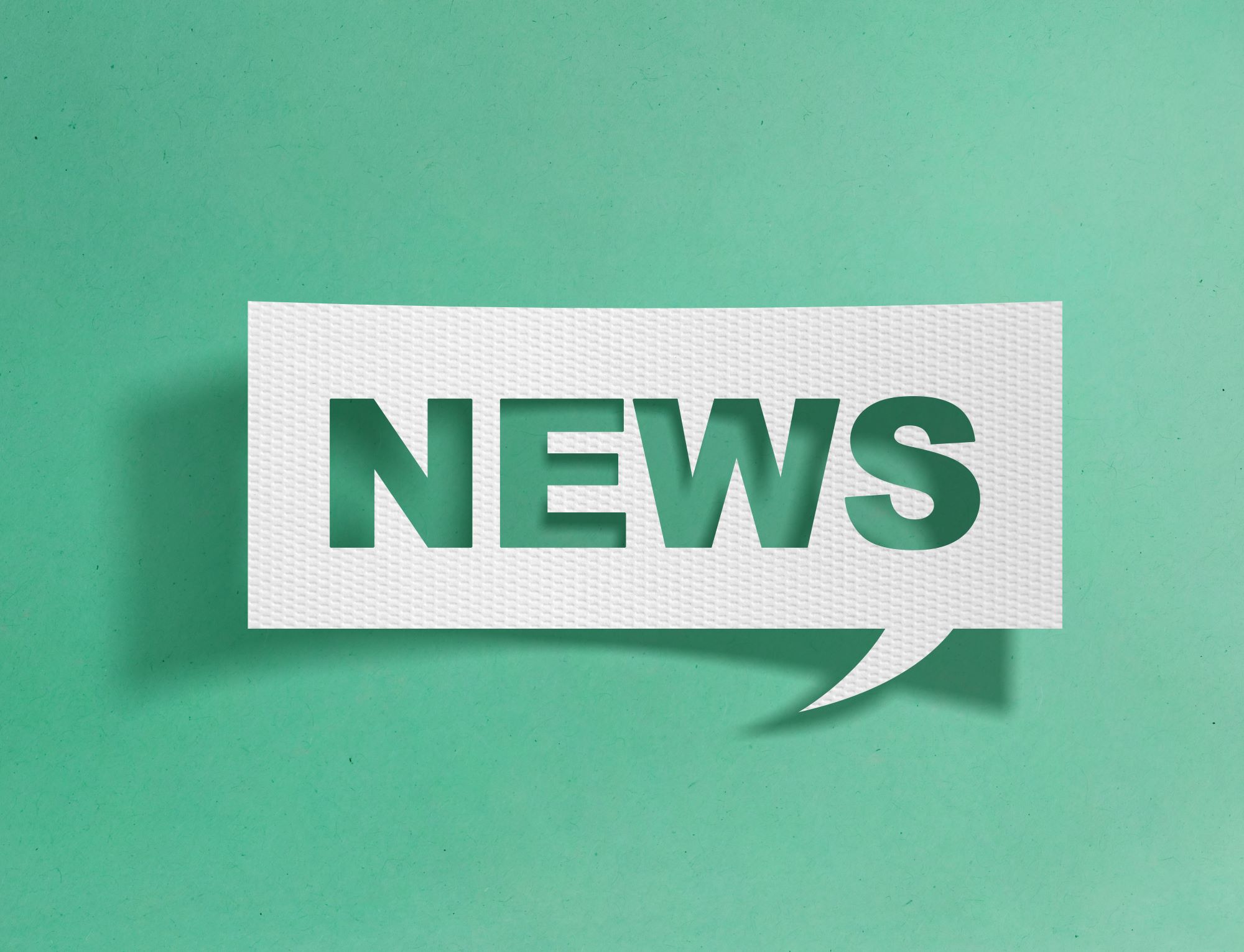
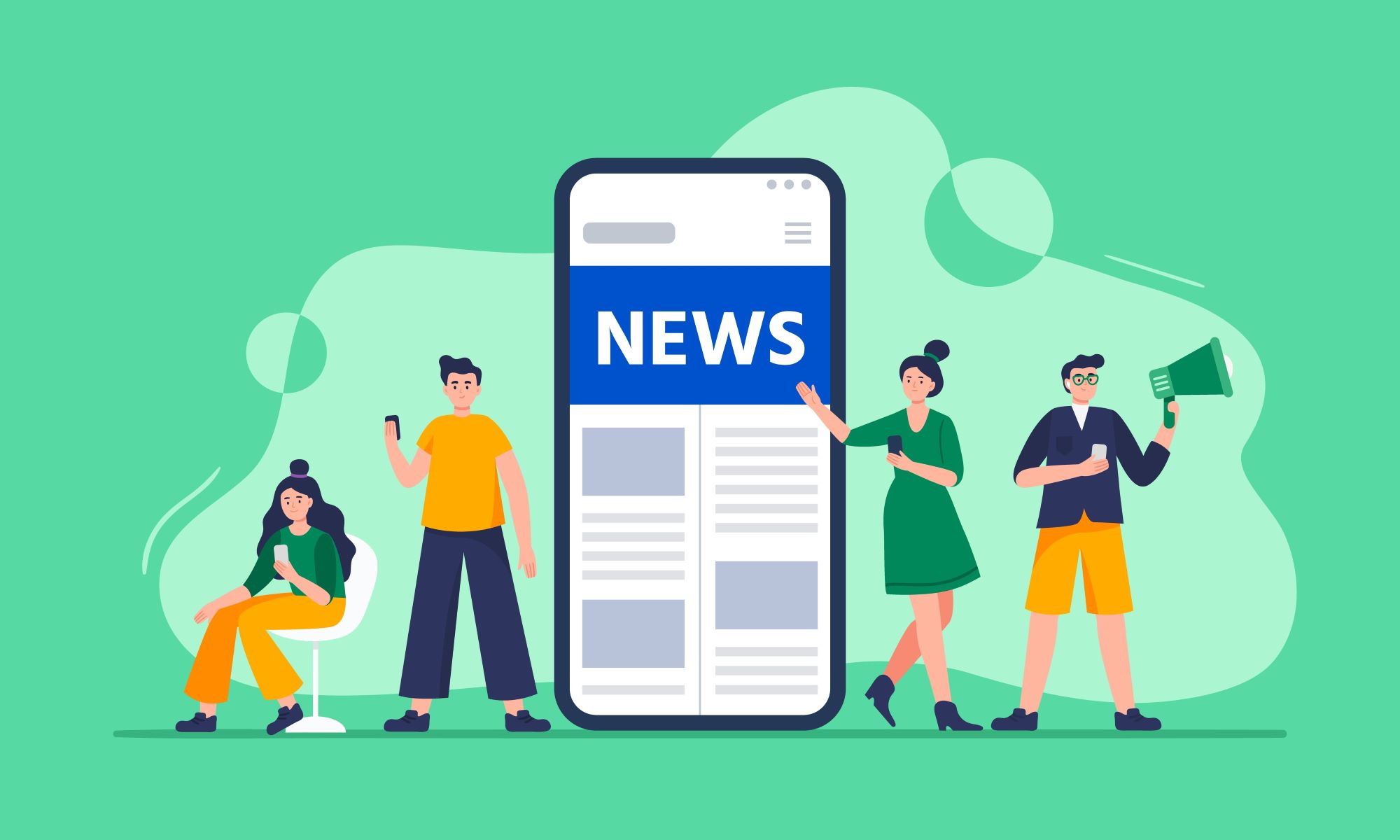
$17.5 million to build domestic supply chain for critical minerals & materials
(NETL to manage the selected projects) Clean Technica 4/24/2024
(NETL to manage the selected projects) Carbon Herald 4/19/2024
NETL’s 2024 Annual Earth Day Art Contest
Energy.gov 4/17/2024
Partner with us
Research Partnerships and Tech Transfer supports NETL and NETL staff in identifying, exploring, and securing opportunities to leverage NETL’s core capabilities and competencies through strategic engagement, collaboration, and partnership with domestic and international government organizations, national laboratories, academia, industry, and other private and public stakeholders.

What We Do




Our Mission
Driving innovation and delivering solutions for an environmentally sustainable and prosperous energy future:
- Ensuring affordable, abundant and reliable energy that drives a robust economy and national security, while
- Developing technologies to manage carbon across the full life cycle, and
- Enabling environmental sustainability for all Americans.
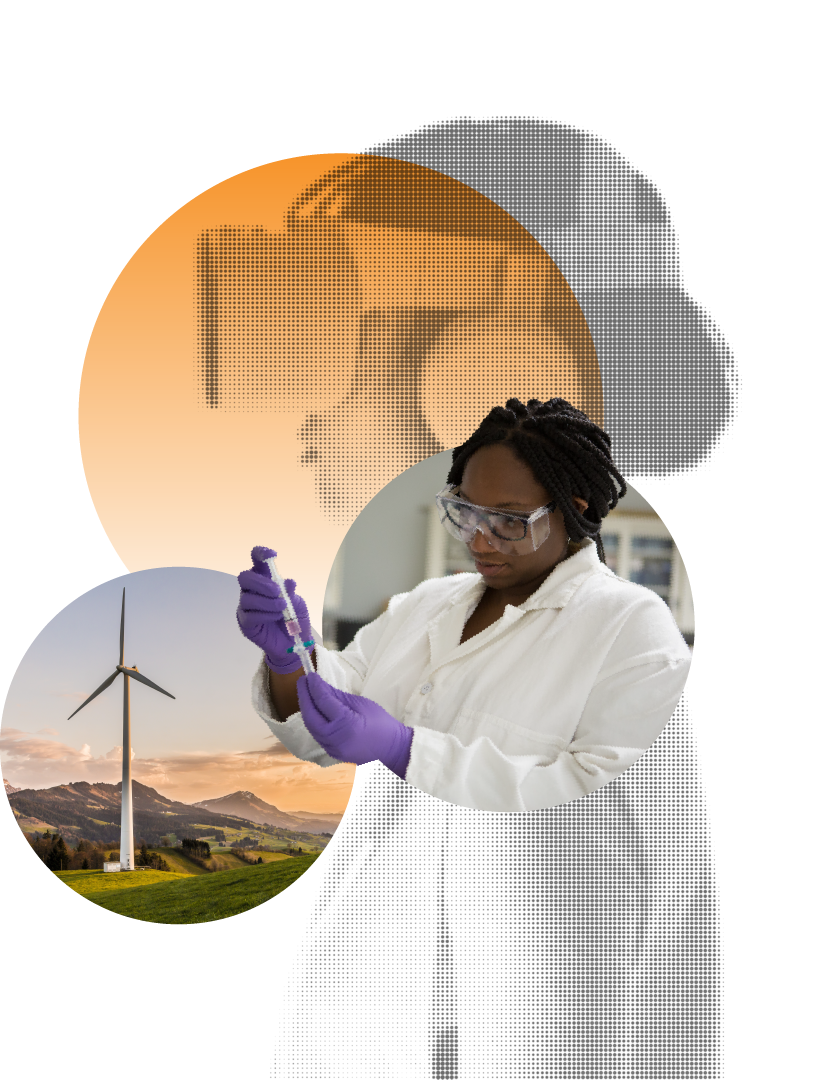